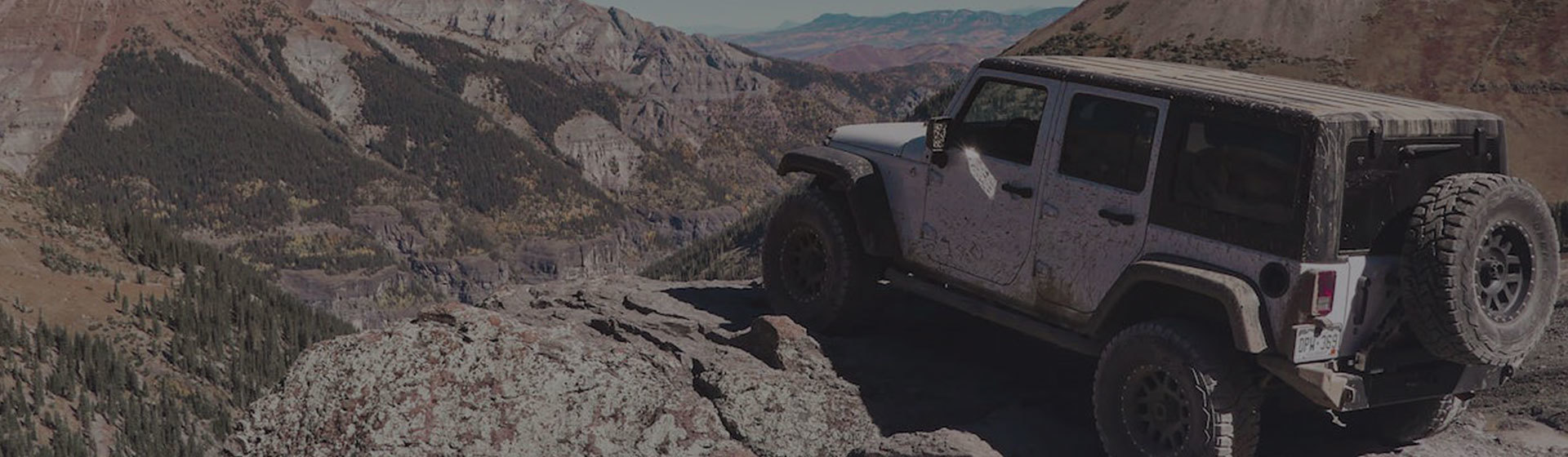
Automobile wheel hub processing technology
Release time:
23 Feb,2023
First, forging process. The forging temperature is controlled between 300℃ and 400℃. The metal materials are shaped by the forging press, and the shape of the metal materials is changed according to the relevant scheme. Combined with practice, the forging process has higher processing efficiency, but there are more production procedures and higher costs.
Second, casting process. There are many types of casting process, and different processes have the characteristics of differentiation. Gravity casting is more traditional, using gravity, filling and other processes to change the shape of liquid metal. This production process is less difficult, mass production can be successfully realized, but it is difficult to ensure the internal quality of the product, prone to serious shrinkage and porosity problems, basically no longer used. Low pressure casting is the process of casting under low pressure mode, which can produce the wheel with high quality in large quantities. Compared with the previous gravity casting process, this method is difficult to utilize metal melting liquid efficiently and has higher production cost. At present, low pressure casting technology has been developed rapidly, which can effectively ensure product quality. Extrusion casting integrates casting and forging process, integrates the advantages of the two processes, does not need high cost, but needs to use precision machining instruments to improve the wheel hub modeling.
Third, 3D printing. The high temperature of forging, casting and other processing technology restricts the use of titanium alloy to a great extent. In recent years, 3D taping technology is gradually mature, which provides good conditions for machining titanium alloy hub. Rapid prototyping of 3D printing technology has obvious advantages and great development potential. At this stage, titanium alloy materials are mainly used in the production of automobile parts, covering a variety of processes such as extrusion, powder melting and bonding injection. Compared with traditional technology, 3D printing technology can control the cost of parts customization and small-batch processing, but 3D materials are expensive.
Related news